സോളിഡീകരണ സമയത്ത് വാതക എൻട്രാപ്മെന്റിലൂടെ രൂപം കൊള്ളുന്ന പൊറോസിറ്റി, കാവിറ്റി-ടൈപ്പ് വിച്ഛേദങ്ങൾ, MIG വെൽഡിങ്ങിലെ ഒരു സാധാരണവും എന്നാൽ ബുദ്ധിമുട്ടുള്ളതുമായ ഒരു വൈകല്യവും നിരവധി കാരണങ്ങളുള്ളതുമാണ്.ഇത് സെമി-ഓട്ടോമാറ്റിക് അല്ലെങ്കിൽ റോബോട്ടിക് ആപ്ലിക്കേഷനുകളിൽ ദൃശ്യമാകാം, രണ്ട് സാഹചര്യങ്ങളിലും നീക്കംചെയ്യലും പുനർനിർമ്മിക്കലും ആവശ്യമാണ് - പ്രവർത്തനരഹിതമായ സമയത്തിനും ചെലവ് വർദ്ധനയ്ക്കും കാരണമാകുന്നു.
സ്റ്റീൽ വെൽഡിങ്ങിലെ സുഷിരത്തിന്റെ പ്രധാന കാരണം വെൽഡിംഗ് പൂളിൽ ഉൾപ്പെടുന്ന നൈട്രജൻ (N2) ആണ്.ലിക്വിഡ് പൂൾ തണുക്കുമ്പോൾ, N2 ന്റെ ലായകത ഗണ്യമായി കുറയുകയും N2 ഉരുകിയ ഉരുക്കിൽ നിന്ന് പുറത്തുവരുകയും കുമിളകൾ (സുഷിരങ്ങൾ) രൂപപ്പെടുകയും ചെയ്യുന്നു.ഗാൽവാനൈസ്ഡ്/ഗാൽവാനിയൽ വെൽഡിങ്ങിൽ, ബാഷ്പീകരിക്കപ്പെട്ട സിങ്ക് വെൽഡിംഗ് പൂളിലേക്ക് ഇളക്കിവിടാം, കുളം ദൃഢമാകുന്നതിന് മുമ്പ് രക്ഷപ്പെടാൻ മതിയായ സമയം ഇല്ലെങ്കിൽ, അത് പോറോസിറ്റി ഉണ്ടാക്കുന്നു.അലുമിനിയം വെൽഡിങ്ങിനായി, സ്റ്റീലിൽ N2 പ്രവർത്തിക്കുന്നതുപോലെ, എല്ലാ സുഷിരങ്ങളും ഹൈഡ്രജൻ (H2) മൂലമാണ് ഉണ്ടാകുന്നത്.
വെൽഡിംഗ് പൊറോസിറ്റി ബാഹ്യമായോ ആന്തരികമായോ പ്രത്യക്ഷപ്പെടാം (പലപ്പോഴും ഉപ-ഉപരിതല പൊറോസിറ്റി എന്ന് വിളിക്കുന്നു).ഇത് വെൽഡിംഗിലോ മുഴുവൻ നീളത്തിലോ ഒരൊറ്റ പോയിന്റിൽ വികസിപ്പിച്ചെടുക്കാം, ഇത് ദുർബലമായ വെൽഡുകളിലേക്ക് നയിക്കുന്നു.
സുഷിരത്തിന്റെ ചില പ്രധാന കാരണങ്ങൾ എങ്ങനെ തിരിച്ചറിയാമെന്നും അവ എങ്ങനെ വേഗത്തിൽ പരിഹരിക്കാമെന്നും അറിയുന്നത് ഗുണനിലവാരവും ഉൽപ്പാദനക്ഷമതയും താഴത്തെ വരിയും മെച്ചപ്പെടുത്താൻ സഹായിക്കും.
മോശം ഷീൽഡിംഗ് ഗ്യാസ് കവറേജ്
അന്തരീക്ഷ വാതകങ്ങളെ (N2, H2) വെൽഡ് പൂളിനെ മലിനമാക്കാൻ അനുവദിക്കുന്നതിനാൽ, വെൽഡിംഗ് പൊറോസിറ്റിയുടെ ഏറ്റവും സാധാരണമായ കാരണം മോശം ഷീൽഡിംഗ് ഗ്യാസ് കവറേജാണ്.മോശം ഷീൽഡിംഗ് ഗ്യാസ് ഫ്ലോ റേറ്റ്, ഗ്യാസ് ചാനലിലെ ചോർച്ച, അല്ലെങ്കിൽ വെൽഡ് സെല്ലിലെ അമിതമായ വായു പ്രവാഹം എന്നിവയുൾപ്പെടെ നിരവധി കാരണങ്ങളാൽ ശരിയായ കവറേജിന്റെ അഭാവം സംഭവിക്കാം.അമിത വേഗതയുള്ള യാത്രാ വേഗതയും ഒരു കുറ്റവാളിയാകാം.
മോശം ഒഴുക്കാണ് പ്രശ്നത്തിന് കാരണമാകുന്നതെന്ന് ഒരു ഓപ്പറേറ്റർ സംശയിക്കുന്നുവെങ്കിൽ, നിരക്ക് മതിയായതാണെന്ന് ഉറപ്പാക്കാൻ ഗ്യാസ് ഫ്ലോ മീറ്റർ ക്രമീകരിക്കാൻ ശ്രമിക്കുക.ഒരു സ്പ്രേ ട്രാൻസ്ഫർ മോഡ് ഉപയോഗിക്കുമ്പോൾ, ഉദാഹരണത്തിന്, മണിക്കൂറിൽ 35 മുതൽ 50 ക്യുബിക് അടി (cfh) ഒഴുക്ക് മതിയാകും.ഉയർന്ന ആമ്പിയറേജിൽ വെൽഡിങ്ങിന് ഫ്ലോ റേറ്റ് വർദ്ധിപ്പിക്കേണ്ടതുണ്ട്, എന്നാൽ നിരക്ക് വളരെ ഉയർന്നതായി സജ്ജീകരിക്കാതിരിക്കേണ്ടത് പ്രധാനമാണ്.ഇത് ഷീൽഡിംഗ് ഗ്യാസ് കവറേജിനെ തടസ്സപ്പെടുത്തുന്ന ചില തോക്ക് ഡിസൈനുകളിൽ പ്രക്ഷുബ്ധതയ്ക്ക് കാരണമാകും.
വ്യത്യസ്തമായി രൂപകൽപ്പന ചെയ്ത തോക്കുകൾക്ക് വ്യത്യസ്ത വാതക പ്രവാഹ സ്വഭാവങ്ങളുണ്ടെന്നത് ശ്രദ്ധിക്കേണ്ടതാണ് (ചുവടെയുള്ള രണ്ട് ഉദാഹരണങ്ങൾ കാണുക).മുകളിലെ രൂപകൽപ്പനയ്ക്കുള്ള ഗ്യാസ് ഫ്ലോ റേറ്റ് "സ്വീറ്റ് സ്പോട്ട്" താഴത്തെ രൂപകൽപ്പനയേക്കാൾ വളരെ വലുതാണ്.വെൽഡ് സെൽ സജ്ജീകരിക്കുമ്പോൾ ഒരു വെൽഡിംഗ് എഞ്ചിനീയർ പരിഗണിക്കേണ്ട കാര്യമാണിത്.
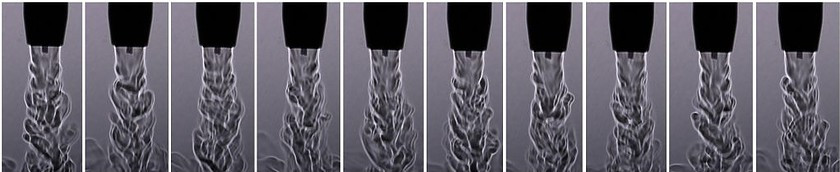
ഡിസൈൻ 1 നോസൽ ഔട്ട്ലെറ്റിൽ സുഗമമായ വാതക പ്രവാഹം കാണിക്കുന്നു
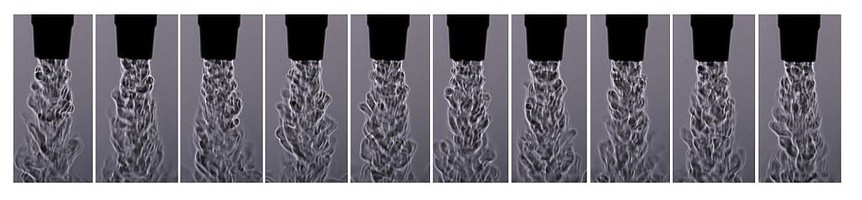
ഡിസൈൻ 2 നോസൽ ഔട്ട്ലെറ്റിൽ പ്രക്ഷുബ്ധമായ വാതക പ്രവാഹം കാണിക്കുന്നു.
ഗ്യാസ് ഹോസ്, ഫിറ്റിംഗുകൾ, കണക്ടറുകൾ, കൂടാതെ MIG വെൽഡിംഗ് തോക്കിന്റെ പവർ പിന്നിലെ ഒ-റിംഗുകൾ എന്നിവയ്ക്ക് കേടുപാടുകൾ ഉണ്ടോയെന്ന് പരിശോധിക്കുക.ആവശ്യാനുസരണം മാറ്റിസ്ഥാപിക്കുക.
വെൽഡ് സെല്ലിലെ ഓപ്പറേറ്റർമാരെയോ ഭാഗങ്ങളെയോ തണുപ്പിക്കാൻ ഫാനുകൾ ഉപയോഗിക്കുമ്പോൾ, ഗ്യാസ് കവറേജിനെ തടസ്സപ്പെടുത്തുന്ന വെൽഡിംഗ് ഏരിയയിലേക്ക് അവ നേരിട്ട് ചൂണ്ടിക്കാണിക്കാതിരിക്കാൻ ശ്രദ്ധിക്കുക.ബാഹ്യ വായു പ്രവാഹത്തിൽ നിന്ന് സംരക്ഷിക്കാൻ വെൽഡ് സെല്ലിൽ ഒരു സ്ക്രീൻ സ്ഥാപിക്കുക.
ശരിയായ ടിപ്പ്-ടു-വർക്ക് ദൂരം ഉണ്ടെന്ന് ഉറപ്പാക്കാൻ റോബോട്ടിക് ആപ്ലിക്കേഷനുകളിൽ പ്രോഗ്രാം വീണ്ടും സ്പർശിക്കുക, ഇത് ആർക്കിന്റെ ആവശ്യമുള്ള ദൈർഘ്യത്തെ ആശ്രയിച്ച് സാധാരണയായി ½ മുതൽ 3/4 ഇഞ്ച് വരെയാണ്.
അവസാനമായി, പോറോസിറ്റി നിലനിൽക്കുകയാണെങ്കിൽ യാത്രയുടെ വേഗത കുറയും അല്ലെങ്കിൽ മികച്ച ഗ്യാസ് കവറേജുള്ള വ്യത്യസ്ത ഫ്രണ്ട് എൻഡ് ഘടകങ്ങൾക്കായി MIG ഗൺ വിതരണക്കാരനെ സമീപിക്കുക
അടിസ്ഥാന ലോഹ മലിനീകരണം
ബേസ് മെറ്റൽ മലിനീകരണമാണ് സുഷിരം ഉണ്ടാകാനുള്ള മറ്റൊരു കാരണം - എണ്ണയും ഗ്രീസും മുതൽ മിൽ സ്കെയിലും തുരുമ്പും വരെ.ഈർപ്പം, പ്രത്യേകിച്ച് അലുമിനിയം വെൽഡിങ്ങിൽ ഈ വിച്ഛേദത്തെ പ്രോത്സാഹിപ്പിക്കും.ഇത്തരത്തിലുള്ള മലിനീകരണം സാധാരണയായി ഓപ്പറേറ്റർക്ക് ദൃശ്യമാകുന്ന ബാഹ്യ സുഷിരത്തിലേക്ക് നയിക്കുന്നു.ഗാൽവാനൈസ്ഡ് സ്റ്റീൽ ഉപരിതല സുഷിരത്തിന് കൂടുതൽ സാധ്യതയുണ്ട്.
ബാഹ്യ പൊറോസിറ്റിയെ ചെറുക്കുന്നതിന്, വെൽഡിങ്ങിന് മുമ്പ് അടിസ്ഥാന മെറ്റീരിയൽ നന്നായി വൃത്തിയാക്കുകയും ഒരു മെറ്റൽ-കോർഡ് വെൽഡിംഗ് വയർ ഉപയോഗിക്കുന്നത് പരിഗണിക്കുകയും ചെയ്യുക.ഈ തരത്തിലുള്ള വയർ സോളിഡ് വയറിനേക്കാൾ ഉയർന്ന അളവിലുള്ള ഡീഓക്സിഡൈസറുകൾ ഉണ്ട്, അതിനാൽ അടിസ്ഥാന മെറ്റീരിയലിൽ അവശേഷിക്കുന്ന ഏതെങ്കിലും മാലിന്യങ്ങളെ ഇത് കൂടുതൽ സഹിഷ്ണുത കാണിക്കുന്നു.ഇവയും മറ്റേതെങ്കിലും വയറുകളും എല്ലായ്പ്പോഴും ചെടിയേക്കാൾ സമാനമായതോ അൽപ്പം ഉയർന്നതോ ആയ താപനിലയുള്ള വരണ്ടതും വൃത്തിയുള്ളതുമായ സ്ഥലത്ത് സൂക്ഷിക്കുക.ഇത് ചെയ്യുന്നത് വെൽഡ് പൂളിലേക്ക് ഈർപ്പം കൊണ്ടുവന്ന് സുഷിരത്തിന് കാരണമാകുന്ന കാൻസൻസേഷൻ കുറയ്ക്കാൻ സഹായിക്കും.ഒരു തണുത്ത വെയർഹൗസിലോ പുറത്തോ വയറുകൾ സൂക്ഷിക്കരുത്.
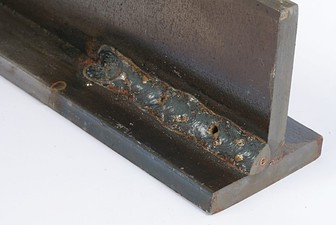
സോളിഡീകരണ സമയത്ത് വാതക എൻട്രാപ്മെന്റിലൂടെ രൂപം കൊള്ളുന്ന പൊറോസിറ്റി, കാവിറ്റി-ടൈപ്പ് വിച്ഛേദങ്ങൾ, MIG വെൽഡിങ്ങിലെ ഒരു സാധാരണവും എന്നാൽ ബുദ്ധിമുട്ടുള്ളതുമായ ഒരു വൈകല്യവും നിരവധി കാരണങ്ങളുള്ളതുമാണ്.
ഗാൽവാനൈസ്ഡ് സ്റ്റീൽ വെൽഡിംഗ് ചെയ്യുമ്പോൾ, ഉരുക്ക് ഉരുകുന്നതിനേക്കാൾ കുറഞ്ഞ താപനിലയിൽ സിങ്ക് ബാഷ്പീകരിക്കപ്പെടുന്നു, വേഗതയേറിയ യാത്രാ വേഗത വെൽഡ് പൂൾ പെട്ടെന്ന് മരവിപ്പിക്കാൻ ഇടയാക്കുന്നു.ഇത് സ്റ്റീലിൽ സിങ്ക് നീരാവി കുടുങ്ങി, അതിന്റെ ഫലമായി സുഷിരങ്ങൾ ഉണ്ടാകുന്നു.യാത്രയുടെ വേഗത നിരീക്ഷിച്ച് ഈ സാഹചര്യത്തെ ചെറുക്കുക.വീണ്ടും, വെൽഡിംഗ് പൂളിൽ നിന്ന് സിങ്ക് നീരാവി രക്ഷപ്പെടാൻ സഹായിക്കുന്ന പ്രത്യേകം രൂപകൽപ്പന ചെയ്ത (ഫ്ലക്സ് ഫോർമുല) മെറ്റൽ-കോർഡ് വയർ പരിഗണിക്കുക.
അടഞ്ഞതും കൂടാതെ/അല്ലെങ്കിൽ വലിപ്പം കുറഞ്ഞതുമായ നോസിലുകൾ
അടഞ്ഞതും കൂടാതെ/അല്ലെങ്കിൽ വലിപ്പം കുറഞ്ഞതുമായ നോസിലുകളും സുഷിരത്തിന് കാരണമാകും.വെൽഡിംഗ് സ്പാറ്റർ നോസിലിലും കോൺടാക്റ്റ് ടിപ്പിന്റെയും ഡിഫ്യൂസറിന്റെയും ഉപരിതലത്തിൽ നിയന്ത്രിത ഷീൽഡിംഗ് വാതക പ്രവാഹത്തിലേക്ക് നയിക്കുന്നു അല്ലെങ്കിൽ അത് പ്രക്ഷുബ്ധമാകാൻ ഇടയാക്കും.രണ്ട് സാഹചര്യങ്ങളും അപര്യാപ്തമായ സംരക്ഷണത്തോടെ വെൽഡ് പൂൾ ഉപേക്ഷിക്കുന്നു.
ഈ സാഹചര്യത്തെ സങ്കീർണ്ണമാക്കുന്നത് പ്രയോഗത്തിന് വളരെ ചെറുതും വലുതും വേഗത്തിലുള്ളതുമായ സ്പാറ്റർ ബിൽഡപ്പിന് കൂടുതൽ സാധ്യതയുള്ളതുമായ ഒരു നോസൽ ആണ്.ചെറിയ നോസിലുകൾക്ക് മികച്ച ജോയിന്റ് ആക്സസ് നൽകാൻ കഴിയും, മാത്രമല്ല വാതക പ്രവാഹത്തിന് അനുവദിച്ചിരിക്കുന്ന ചെറിയ ക്രോസ്-സെക്ഷണൽ ഏരിയ കാരണം വാതക പ്രവാഹത്തെ തടസ്സപ്പെടുത്തുകയും ചെയ്യും.നോസൽ സ്റ്റിക്ക്ഔട്ടിലേക്കുള്ള (അല്ലെങ്കിൽ ഇടവേള) കോൺടാക്റ്റ് ടിപ്പിന്റെ വേരിയബിൾ എപ്പോഴും മനസ്സിൽ വയ്ക്കുക, കാരണം ഇത് നിങ്ങളുടെ നോസൽ തിരഞ്ഞെടുക്കലിലൂടെ വാതക പ്രവാഹത്തെയും സുഷിരത്തെയും സംരക്ഷിക്കുന്നതിനെ ബാധിക്കുന്ന മറ്റൊരു ഘടകമാകാം.
അത് മനസ്സിൽ വെച്ചുകൊണ്ട്, നോസൽ ആപ്ലിക്കേഷന് ആവശ്യത്തിന് വലുതാണെന്ന് ഉറപ്പാക്കുക.സാധാരണഗതിയിൽ, വലിയ വയർ വലുപ്പങ്ങൾ ഉപയോഗിക്കുന്ന ഉയർന്ന വെൽഡിംഗ് കറന്റുള്ള ആപ്ലിക്കേഷനുകൾക്ക് വലിയ ബോർ വലുപ്പമുള്ള ഒരു നോസൽ ആവശ്യമാണ്.
സെമി-ഓട്ടോമാറ്റിക് വെൽഡിംഗ് ആപ്ലിക്കേഷനുകളിൽ, ഇടയ്ക്കിടെ നോസിലിൽ വെൽഡിംഗ് സ്പാറ്റർ പരിശോധിക്കുകയും വെൽഡർ പ്ലയർ (വെൽപ്പറുകൾ) ഉപയോഗിച്ച് നീക്കം ചെയ്യുക അല്ലെങ്കിൽ ആവശ്യമെങ്കിൽ നോസൽ മാറ്റിസ്ഥാപിക്കുക.ഈ പരിശോധനയ്ക്കിടെ, കോൺടാക്റ്റ് ടിപ്പ് നല്ല രൂപത്തിലാണെന്നും ഗ്യാസ് ഡിഫ്യൂസറിന് വ്യക്തമായ ഗ്യാസ് പോർട്ടുകൾ ഉണ്ടെന്നും സ്ഥിരീകരിക്കുക.ഓപ്പറേറ്റർമാർക്ക് ആന്റി-സ്പാറ്റർ സംയുക്തവും ഉപയോഗിക്കാം, പക്ഷേ സംയുക്തത്തിന്റെ അമിതമായ അളവ് ഷീൽഡിംഗ് ഗ്യാസിനെ മലിനമാക്കുകയും നോസൽ ഇൻസുലേഷനെ തകരാറിലാക്കുകയും ചെയ്യുന്നതിനാൽ, കോമ്പൗണ്ടിലേക്ക് നോസൽ വളരെ ദൂരെയോ ദീർഘനേരം മുക്കാതിരിക്കാൻ അവർ ശ്രദ്ധിക്കണം.
ഒരു റോബോട്ടിക് വെൽഡിംഗ് ഓപ്പറേഷനിൽ, സ്പാറ്റർ ബിൽഡപ്പിനെ ചെറുക്കുന്നതിന് ഒരു നോസൽ ക്ലീനിംഗ് സ്റ്റേഷനിലോ റീമറിലോ നിക്ഷേപിക്കുക.ഈ പെരിഫറൽ ഉൽപാദനത്തിലെ പതിവ് ഇടവേളകളിൽ നോസലും ഡിഫ്യൂസറും വൃത്തിയാക്കുന്നു, അങ്ങനെ അത് സൈക്കിൾ സമയത്തെ ബാധിക്കില്ല.നോസൽ ക്ലീനിംഗ് സ്റ്റേഷനുകൾ ഒരു ആന്റി-സ്പാറ്റർ സ്പ്രേയറുമായി ചേർന്ന് പ്രവർത്തിക്കാൻ ഉദ്ദേശിച്ചുള്ളതാണ്, ഇത് മുൻഭാഗത്തെ ഘടകങ്ങളിലേക്ക് സംയുക്തത്തിന്റെ നേർത്ത കോട്ട് പ്രയോഗിക്കുന്നു.വളരെയധികം അല്ലെങ്കിൽ വളരെ കുറച്ച് ആന്റി-സ്പാറ്റർ ദ്രാവകം അധിക സുഷിരത്തിന് കാരണമാകും.നോസൽ ക്ലീനിംഗ് പ്രക്രിയയിൽ എയർ ബ്ലാസ്റ്റ് ചേർക്കുന്നത് ഉപഭോഗവസ്തുക്കളിൽ നിന്ന് അയഞ്ഞ സ്പാറ്റർ മായ്ക്കാനും സഹായിക്കും.
ഗുണനിലവാരവും ഉൽപ്പാദനക്ഷമതയും നിലനിർത്തുന്നു
വെൽഡിംഗ് പ്രക്രിയ നിരീക്ഷിക്കാനും സുഷിരത്തിന്റെ കാരണങ്ങൾ അറിയാനും ശ്രദ്ധിക്കുന്നതിലൂടെ, പരിഹാരങ്ങൾ നടപ്പിലാക്കുന്നത് താരതമ്യേന ലളിതമാണ്.അങ്ങനെ ചെയ്യുന്നത് കൂടുതൽ ആർക്ക്-ഓൺ സമയവും ഗുണനിലവാരമുള്ള ഫലങ്ങളും ഉൽപ്പാദനത്തിലൂടെ നീങ്ങുന്ന കൂടുതൽ നല്ല ഭാഗങ്ങളും ഉറപ്പാക്കാൻ സഹായിക്കും.
പോസ്റ്റ് സമയം: ഫെബ്രുവരി-02-2020